

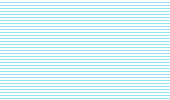

![]()
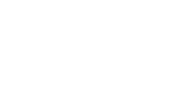
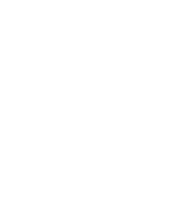
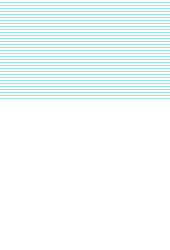
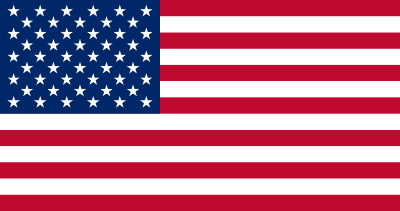
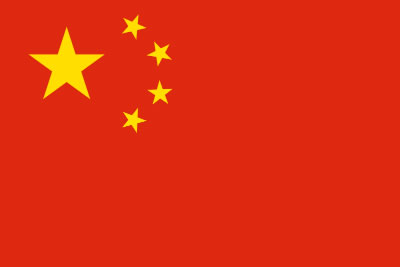
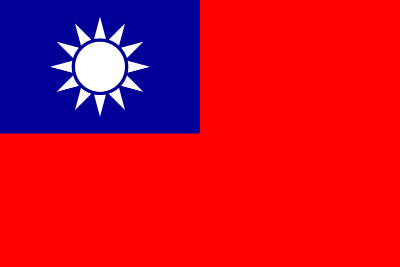
Extruded Rubber Profiles
Whether you are in need of common Neoprene Tubing/Cord, or a complex custom Extruded Rubber Profile such as J seals, P seals, D seals or Lip seals and so on. Chiao Ying Rubber has the expertise and equipment to be your supplier of choice.
Chiao Ying Rubber team has the rubber industry experience and production savvy to understand and meet your quality and delivery requirements. Our extruded profile finds variety of application in Electronics, Machines/ Systems, Automotive and Building & Construction industries. Chiao Ying offer these rubber products at the most competitive prices.
The available of a full range of rubber material compounds including: NR, IR, SBR, IIR, EPDM, CR, PU, Silicone, Fluorocarbon Rubber (e.g. Viton) and Fluorosilicone.
The Extrusion Manufacturing Processes including:
* Tubing
Chiao Ying Rubber produces different tube cross-sections with a range of inside
hollow diameters and a varying wall thickness to create the desired outside
diameters in a variety of colors, sizes shapes and continuous lengths.
One of our strengths is its large variety of extruders that can deliver a wide range
of sizes, shapes and materials without having any capacity constraints.
* Striping
The company has the ability to deliver strip materials with width and thickness in
almost any configuration.
* Splicing
While splicing is a common capability that takes two pieces of material and joins
them together, Chiao Ying Rubber's splicing methodology and know how are ready
to meet customers' requirements.
* Molded Corner
Molded corner is the product making by extruded door seal by cutting to length
and molding the corner by vulcanization. Large size seals and gaskets are our
specialty.
* Sponge & Foam Extrusion
* Lathe-cut
Lathe-cut is the way to manufacture the flat gasket by saving tooling charge for
molding. There are three ways to making flat gaskets:
1) By compression molding, such way of manufacturing needs a higher tooling
expense for the mold.
2) By extruding and lathe-cut, such way of manufacturing has cost effect, but
short length less than 3.0mm not easy to control the tolerance. Big sizes the
tube possibly collapse during extruding and became over shape.
3) By molding the tube and lathe-cut, such way of manufacturing always used for
making big ID gasket. There are few ways of lathe-cut depending the type of
parts needed. It could be either extruded tube or molded type to cut. Die-cut
the sheet for seal is also available.
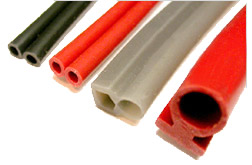
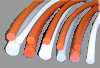
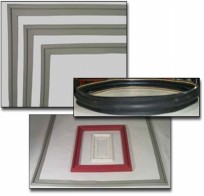
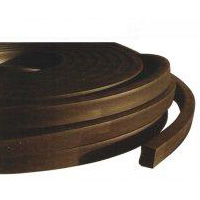
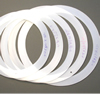